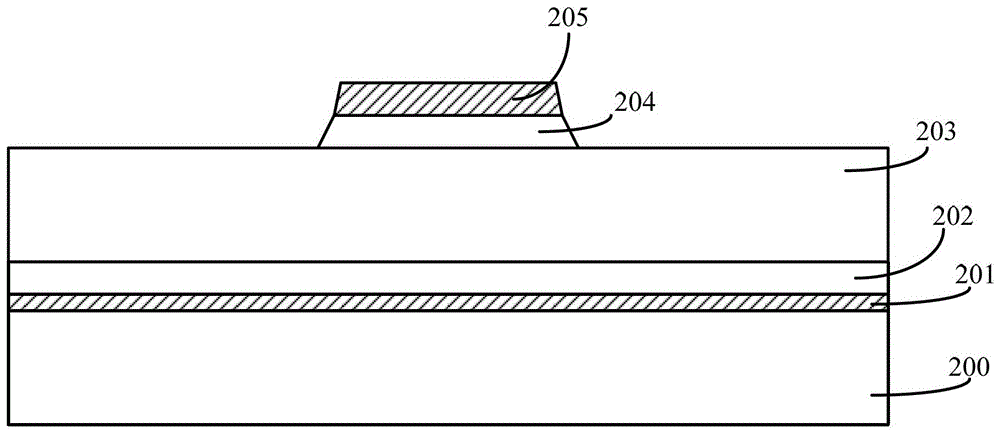
本發(fā)明涉及半導(dǎo)體制造技術(shù)領(lǐng)域,尤其涉及一種半導(dǎo)體結(jié)構(gòu)的形成方法。
背景技術(shù):隨著集成電路制造技術(shù)的快速發(fā)展,促使集成電路中的半導(dǎo)體器件,尤其是MOS(MetalOxideSemiconductor,金屬-氧化物-半導(dǎo)體)器件的尺寸不斷地縮小,以此滿足集成電路發(fā)展的小型化和集成化的要求。在MOS晶體管器件的尺寸持續(xù)縮小的過程中,現(xiàn)有工藝以氧化硅或氮氧化硅作為柵介質(zhì)層的工藝受到了挑戰(zhàn)。以氧化硅或氮氧化硅作為柵介質(zhì)層所形成的晶體管出現(xiàn)了一些問題,包括漏電流增加以及雜質(zhì)的擴散,從而影響晶體管的閾值電壓,進而影響半導(dǎo)體器件的性能。為解決以上問題,含有高K柵介質(zhì)層和金屬柵的晶體管被提出。在所述含有高K柵介質(zhì)層和金屬柵的晶體管中,采用高K(介電常數(shù))材料代替常用的氧化硅或氮氧化硅柵介質(zhì)材料,能夠縮小晶體管尺寸,避免漏電流的產(chǎn)生,并提高晶體管的性能?,F(xiàn)有技術(shù)的具有高K柵介質(zhì)層和金屬柵的晶體管的平面結(jié)構(gòu)示意圖如圖1所示,包括:位于半導(dǎo)體襯底100表面的第一介質(zhì)層105,所述第一介質(zhì)層105內(nèi)具有暴露出半導(dǎo)體襯底100表面的開口(未示出);位于所述開口的底部表面的高K柵介質(zhì)層101;位于所述高K柵介質(zhì)層101表面的金屬柵極層103;位于高K柵介質(zhì)層101和金屬柵極層103兩側(cè)的半導(dǎo)體襯底100表面的側(cè)墻104;位于高K柵介質(zhì)層101、金屬柵極層103和側(cè)墻104兩側(cè)的半導(dǎo)體襯底100內(nèi)的源區(qū)106a和漏區(qū)106b。然而,隨著晶體管的尺寸持續(xù)縮小,晶體管的尺寸難以精確控制,導(dǎo)致半導(dǎo)體器件性能的不穩(wěn)定。更多關(guān)于具有高K柵介質(zhì)層和金屬柵的晶體管或其形成工藝的相關(guān)資料請參考公開號為US2011/0195549的美國專利文件。
技術(shù)實現(xiàn)要素:本發(fā)明解決的問題是提供一種半導(dǎo)體結(jié)構(gòu)的形成方法,能夠精確控制晶體管中的柵極層的特征尺寸,保證了晶體管及半導(dǎo)體器件的性能穩(wěn)定。為解決上述問題,本發(fā)明提供一種半導(dǎo)體結(jié)構(gòu)的形成方法,包括:提供半導(dǎo)體襯底,所述半導(dǎo)體襯底表面具有停止層,所述停止層表面具有柵極薄膜,所述柵極薄膜的部分表面具有第一掩膜層,所述第一掩膜層表面具有第二掩膜層,所述第二掩膜層的材料和停止層的材料相同,所述第一掩膜層和第二掩膜層的材料不同;在所述第一掩膜層的側(cè)壁表面形成保護層,所述保護層的材料與第二掩膜層和停止層的材料相同;在形成所述保護層之后,以第二掩膜層為掩膜刻蝕所述柵極薄膜,至暴露出停止層表面為止,形成柵極層??蛇x的,所述第一掩膜層的材料為氮化硅,所述第二掩膜層、保護層和停止層的材料為氧化硅,所述柵極薄膜的材料為多晶硅??蛇x的,所述保護層的形成工藝為等離子處理,所述等離子處理工藝包括:壓力2毫托~100毫托,等離子體解離功率為100瓦~1500瓦,偏置電壓0~50V,氣體包含O2,氣體總流量1標準毫升/分鐘~1000標準毫升/分鐘,反應(yīng)時間5秒~200秒??蛇x的,所述保護層的厚度為1埃~100埃??蛇x的,還包括:在形成所述柵極層之后,去除所述第二掩膜層,并在所述柵極層和第一掩膜層兩側(cè)的半導(dǎo)體襯底表面形成側(cè)墻??蛇x的,以所述側(cè)墻和第一掩膜層為掩膜對半導(dǎo)體襯底進行離子注入,在柵極層兩側(cè)的半導(dǎo)體襯底內(nèi)形成源區(qū)和漏區(qū)??蛇x的,還包括:在所述停止層表面形成柵介質(zhì)薄膜;在所述柵介質(zhì)薄膜表面形成柵極薄膜;在刻蝕所述柵極薄膜形成柵極層時,刻蝕所述柵介質(zhì)薄膜,形成柵介質(zhì)層??蛇x的,所述柵介質(zhì)薄膜的材料為高K介質(zhì)材料??蛇x的,還包括:在所述柵介質(zhì)薄膜表面形成覆蓋薄膜,所述覆蓋薄膜的材料為氮化鉭或氮化鈦;在所述覆蓋薄膜表面形成柵極薄膜;在刻蝕所述柵極薄膜形成柵極層時,刻蝕所述覆蓋薄膜,形成覆蓋層??蛇x的,還包括:在形成所述柵極層之后,在所述半導(dǎo)體襯底表面形成介質(zhì)層,所述介質(zhì)層的表面與第一掩膜層的表面齊平;在形成介質(zhì)層之后,去除所述第一掩膜層和柵極層,形成開口;在所述開口內(nèi)形成金屬柵??蛇x的,所述第一掩膜層和第二掩膜層的形成工藝包括:在所述柵極層薄膜表面形成第一掩膜薄膜;在所述第一掩膜薄膜表面形成第二掩膜薄膜;在所述第二掩膜薄膜表面形成第一光刻膠層;以所述第一光刻膠層為掩膜,刻蝕所述第二掩膜薄膜和第一掩膜薄膜,直至暴露出柵極薄膜為止??蛇x的,還包括:在刻蝕所述柵極薄膜之前,在所述第二掩膜層表面形成第二光刻膠層;以所述第二光刻膠層和第二掩膜層為掩膜,刻蝕所述柵極薄膜,形成柵極層。與現(xiàn)有技術(shù)相比,本發(fā)明的技術(shù)方案具有以下優(yōu)點:所述柵極薄膜表面具有第一掩膜層,所述第一掩膜層表面具有第二掩膜層;其中,所述第一掩膜層作為后續(xù)形成側(cè)墻時的掩膜,所述第二掩膜層作為刻蝕柵極薄膜的掩膜;在所述第一掩膜層的側(cè)壁表面形成保護層,且所述保護層的材料與第二掩膜層相同;由于所述第二掩膜層作為刻蝕柵極薄膜的掩膜,所述刻蝕柵極薄膜的工藝對于所述第二掩膜層具有較低的刻蝕速率,因此所述刻蝕工藝對所述保護層的刻蝕速率也較低;所述保護層能夠保護所述第一掩膜層在刻蝕柵極薄膜的工藝中不被減薄,從而保證了后續(xù)刻蝕形成的柵極層時,所形成的柵極層不會因為第一掩膜層的減薄而尺寸縮小,能夠使所形成的柵極層的尺寸符合設(shè)計標準;因此,所述柵極層的特征尺寸精確易控,使所形成的晶體管的特征尺寸標準精確,所形成的半導(dǎo)體器件的性能穩(wěn)定良好。進一步的,所述保護層的形成工藝為等離子處理工藝,所述等離子處理工藝的氣體為氧氣;在所述等離子處理工藝中,氧氣被解離成為等離子體,并通過工藝參數(shù)的調(diào)節(jié),使氧氣等離子體帶有足夠高的能量;由于第一掩膜層的材料為氮化硅,使所述氧氣等離子體所帶有的能量能夠破壞氮化硅的化學(xué)鍵,在所述等離子體處理工藝中,所述第一掩膜層的側(cè)壁表面能夠產(chǎn)生硅離子和氮離子;繼而,氧離子替代氮離子與所述硅離子構(gòu)成氧化硅材料,而被替代的氮離子隨著工藝過程中的氣流被帶走。而且,所述等離子處理工藝能夠使所注入的氧氣等離子體積聚于所述第一掩膜層的側(cè)壁表面,更易于使氧離子與氮化硅中的硅離子生成氧化硅,同時,使所形成的氧化硅厚度薄,即保護層的厚度薄,不會增大后續(xù)所形成的柵極層的尺寸,使所形成的柵極層的尺寸精確。附圖說明圖1是現(xiàn)有技術(shù)的具有高K柵介質(zhì)層和金屬柵的晶體管的剖面結(jié)構(gòu)示意圖;圖2至圖3是一種形成如圖1所示晶體管的部分過程的剖面結(jié)構(gòu)示意圖;圖4至圖9是本發(fā)明的實施例所述的半導(dǎo)體結(jié)構(gòu)的形成方法的形成過程的剖面結(jié)構(gòu)示意圖。具體實施方式如背景技術(shù)所述,隨著晶體管的尺寸持續(xù)縮小,晶體管的尺寸難以精確控制,導(dǎo)致半導(dǎo)體器件性能的不穩(wěn)定。圖2至圖3是一種形成如圖1所示晶體管的部分過程的剖面結(jié)構(gòu)示意圖,包括:請參考圖2,在半導(dǎo)體襯底200表面形成氧化硅薄膜201、位于氧化硅薄膜201表面的高K介質(zhì)薄膜202和位于高K介質(zhì)薄膜202表面的多晶硅薄膜203;在所述多晶硅薄膜203表面形成氮化硅層204、以及位于氮化硅層204表面的氧化硅層205。其中,所述多晶硅薄膜203用于形成偽柵極層,所述偽柵極層為后續(xù)形成的金屬柵占據(jù)空間位置;所述氮化硅層204用于在后續(xù)形成側(cè)墻時作為掩膜,保護偽柵極層的形貌不被破壞;所述氧化硅層205用于作為刻蝕形成偽柵極層和柵介質(zhì)層的掩膜;所述氧化硅薄膜201用于定義刻蝕多晶硅薄膜203和高K介質(zhì)薄膜202工藝的停止位置,避免半導(dǎo)體襯底200表面受到損傷。請參考圖3,以所述氧化硅層205為掩膜刻蝕所述多晶硅薄膜203(如圖2所示)和高K介質(zhì)薄膜202(如圖2所示),所述多晶硅薄膜203形成偽柵極層203a,所述高K介質(zhì)薄膜202形成柵介質(zhì)層202a。當形成所述偽柵極層203a之后,去除所述氧化硅層205,并以所述氮化硅層204為掩膜,在所述偽柵極層203a兩側(cè)的氧化硅薄膜201表面形成側(cè)墻(未示出),并在側(cè)墻兩側(cè)的半導(dǎo)體襯底200內(nèi)形成源區(qū)和漏區(qū);后續(xù)再以金屬材料替代所述偽柵極層203a,形成金屬柵,以完成晶體管的制造。經(jīng)過本發(fā)明的發(fā)明人研究發(fā)現(xiàn),為了使所述刻蝕工藝停止于氧化硅薄膜201,所述刻蝕工藝需要保證對于氧化硅具有較高的選擇性,即刻蝕氧化硅的速率較慢,從而能夠保證氧化硅層205的形貌在刻蝕多晶硅薄膜203時不會改變,而且所述刻蝕工藝能夠停止于氧化硅薄膜201。然而,當保證了所述刻蝕工藝對于刻蝕氧化硅的速率較慢時,難以同時兼顧對于氮化硅層204的刻蝕選擇性,往往會導(dǎo)致刻蝕所述氮化硅層204的速率較快,進而導(dǎo)致所述氮化硅層204的側(cè)壁被減??;而一旦所述氮化硅層204被減薄,容易導(dǎo)致刻蝕形成的偽柵極層203a的尺寸相對于設(shè)計尺寸變?。ㄈ鐖D3的虛線所示,為偽柵極層203a為設(shè)計尺寸時的形貌剖面圖形),因此使偽柵極層203a的特征尺寸難以精確控制,進而導(dǎo)致后續(xù)所形成的金屬柵以及整個晶體管的尺寸不精確,尤其是當所述晶體管的特征尺寸進一步縮小時,所述尺寸的不精確對于半導(dǎo)體器件的性能影響更為顯著。經(jīng)過本發(fā)明的發(fā)明人進一步研究,在用于形成偽柵極層的柵極薄膜表面形成第一掩膜層、以及位于第一掩膜層表面的第二掩膜層后,在所述第一掩膜層的側(cè)壁表面形成保護層;其中,所述第一掩膜層作為后續(xù)形成側(cè)墻時的掩膜,所述第二掩膜層作為刻蝕柵極薄膜的掩膜,因此,后續(xù)刻蝕柵極薄膜的工藝對于所述第二掩膜層的刻蝕速率較低;使所述保護層的材料與第二掩膜層相同,因此所述保護層在后續(xù)刻蝕柵極薄膜的工藝中,具有較高的刻蝕選擇性,即后續(xù)的刻蝕工藝刻蝕保護層的速率較慢;因此,所述保護層能夠保護所述第一掩膜層在所述刻蝕工藝中不被減薄,進而保證了刻蝕后的柵極層的尺寸符合設(shè)計標準,使所述柵極層的特征尺寸精確,所述半導(dǎo)體器件的性能穩(wěn)定且良好。為使本發(fā)明的上述目的、特征和優(yōu)點能夠更加明顯易懂,下面結(jié)合附圖對本發(fā)明的具體實施方式做詳細的說明。圖4至圖9是本發(fā)明的實施例所述的半導(dǎo)體結(jié)構(gòu)的形成方法的形成過程的剖面結(jié)構(gòu)示意圖。請參考圖4,提供半導(dǎo)體襯底300,所述半導(dǎo)體襯底300表面具有停止層301,所述停止層301表面具有柵介質(zhì)薄膜302,所述柵介質(zhì)薄膜302表面具有柵極薄膜303,所述柵極層薄膜303表面具有第一掩膜薄膜304,所述第一掩膜薄膜304表面具有第二掩膜薄膜305,第二掩膜薄膜305的材料和停止層301的材料相同,所述第一掩膜薄膜304和第二掩膜薄膜305的材料不同。所述半導(dǎo)體襯底300用于為后續(xù)工藝提供工作平臺;所述半導(dǎo)體襯底300為硅襯底、硅鍺襯底、碳化硅襯底、絕緣體上硅(SOI)襯底、絕緣體上鍺(GOI)襯底、玻璃襯底或III-V族化合物襯底(例如砷化鎵等)。在本實施例中,所形成的半導(dǎo)體結(jié)構(gòu)用于形成具有高K柵介質(zhì)層和金屬柵極層的晶體管,所述具有高K柵介質(zhì)層和金屬柵極層的晶體管的尺寸小,有利于半導(dǎo)體器件的微型化和集成化,然而,由于尺寸小,使形成所述晶體管時特征尺寸更加難以精確控制;所述停止層301的材料為氧化硅,所述柵介質(zhì)薄膜302的材料為高K介質(zhì)材料,所述柵極層薄膜303的材料為多晶硅;所述停止層301用于定義后續(xù)刻蝕柵極薄膜303的停止位置,避免半導(dǎo)體襯底300在刻蝕工藝中受到損傷;其次,所述停止層301還能夠用于增強所述柵介質(zhì)薄膜302和半導(dǎo)體襯底300之間的結(jié)合力,減少漏電流的產(chǎn)生;再次,所述停止層301還能夠在后續(xù)采用離子注入形成晶體管的源區(qū)和漏區(qū)時,保護半導(dǎo)體襯底300表面不受損傷。所述柵介質(zhì)薄膜302用于形成晶體管的柵介質(zhì)層,所述柵極層薄膜303用于形成晶體管的偽柵極層,所述偽柵極層為后續(xù)形成的金屬柵占據(jù)空間和位置,最終形成具有高K柵介質(zhì)層和金屬柵極層的晶體管。所述第一掩膜薄膜304用于形成第一掩膜層,所述第二掩膜薄膜305用于形成第二掩膜層;所述第一掩膜層用于在后續(xù)形成側(cè)墻時保護所形成的柵極層表面不受損傷、且形貌良好;所述第二掩膜層用于在后續(xù)刻蝕柵極薄膜303時作為掩膜;本實施例中,所述第一掩膜薄膜304的材料為氮化硅,所述第二掩膜薄膜305的材料為氧化硅;其中,由于氮化硅的硬度較大,在形成側(cè)墻時,對柵極層的保護能力更強;由于所述第二掩膜層為后續(xù)刻蝕柵極薄膜303的掩膜,而所述停止層301用于定義所述刻蝕柵極薄膜303工藝的停止位置,因此所述停止層301和第二掩膜薄膜305需要在后續(xù)的刻蝕工藝中具有較高的刻蝕選擇性,以保證刻蝕形成的柵極層尺寸標準精確,且不會受到損傷。在本實施例中,所述停止層301和第二掩膜薄膜305的材料均為氧化硅,因此需要使后續(xù)的刻蝕工藝對于氧化硅具有較高的刻蝕選擇性。此外,后續(xù)形成柵極層之后,需要去除第二掩膜層,并保留第一掩膜層作為形成側(cè)墻的掩膜,因此所述第一掩膜薄膜304的材料與第二掩膜薄膜305的材料不同,在本實施例中,所述第一掩膜薄膜304的材料為氮化硅。所述停止層301、柵介質(zhì)薄膜302、柵極薄膜303、第一掩膜薄膜304和第二掩膜薄膜305的形成工藝為沉積工藝,較佳的是化學(xué)氣相沉積工藝;所述停止層301、柵介質(zhì)薄膜302、柵極薄膜303、第一掩膜薄膜304和第二掩膜薄膜305的厚度根據(jù)具體的工藝需求而定,不應(yīng)過于限定。在一實施例中,所述柵介質(zhì)薄膜302表面還形成有覆蓋薄膜(未示出),在所述覆蓋薄膜表面形成柵極薄膜303,所述覆蓋薄膜的材料為氮化鉭或氮化鈦;所述覆蓋薄膜用于形成覆蓋層,所述覆蓋層用于提高后續(xù)形成的柵介質(zhì)層和金屬柵之間的隔離效果,并防止后續(xù)工藝過程中,雜質(zhì)污染通過柵介質(zhì)層擴散入金屬柵中。在另一實施例中,所述柵介質(zhì)薄膜為氧化硅,則在后續(xù)工藝中刻蝕柵極薄膜以形成柵極層,并形成側(cè)墻、源區(qū)和漏區(qū)之后,即形成晶體管。請參考圖5,在所述第二掩膜薄膜305(如圖4所示)表面形成第一光刻膠層306;以所述第一光刻膠層306為掩膜,刻蝕所述第二掩膜薄膜305和第一掩膜薄膜304(如圖4所示),直至暴露出柵極薄膜303為止,形成第二掩膜層305a和第一掩膜層304a。所述第一光刻膠層306用于定義需要形成柵極層的位置;此外,所述第二掩膜薄膜305和第一光刻膠層306之間還具有底部抗反射層(未示出),所述第一光刻膠層306形成于所述底部抗反射層表面,所述底部抗反射層的形成工藝為沉積工藝;所述第一光刻膠層306的形成工藝為:采用旋涂工藝形成第一光刻膠薄膜;采用曝光工藝圖形化所述第一光刻膠薄膜,使所述第一光刻膠層306僅覆蓋需要后續(xù)形成柵極層的對應(yīng)位置。所述刻蝕第二掩膜薄膜305和第一掩膜薄膜304的工藝為各向異性的干法刻蝕工藝;所述各向異性的干法刻蝕工藝能夠通過控制工藝參數(shù),使所形成的第一掩膜層304a和第二掩膜層305a的側(cè)壁垂直于柵極薄膜303表面,或者使所述第一掩膜層304a和第二掩膜層305a的側(cè)壁相對于柵極薄膜303表面傾斜;所述第一掩膜層304a和第二掩膜層305a側(cè)壁的形貌根據(jù)具體工藝需求而定,在本實施例中,所述第一掩膜層304a和第二掩膜層305a的側(cè)壁相對于柵極薄膜303表面傾斜。在完成所述刻蝕工藝之后,采用濕法清洗工藝去除所述第一光刻膠層306、以及底部抗反射層;由于本實施例中需要形成的晶體管尺寸極小,因此,在完成刻蝕第二掩膜薄膜305和第一掩膜薄膜304工藝之后,所述第一光刻膠層306已不能滿足后續(xù)繼續(xù)刻蝕形成柵極層的工藝,難以保證所述第二掩膜層305a表面在后續(xù)形成柵極層的工藝過程中不受損傷,而一旦所述第二掩膜層305a的形貌或尺寸難以保證,會影響所形成的柵極層及晶體管的特征尺寸精確度,繼而影響半導(dǎo)體器件的性能。因此,在形成第一掩膜層304a和第二掩膜層305a之后,需要去除所述第一光刻膠層306,并再次形成光刻膠層作為后續(xù)刻蝕工藝的掩膜,而再次形成的光刻膠層的尺寸精確且形貌良好,能夠保證刻蝕形成的柵極層的特征尺寸精確易控。請參考圖6,在所述第一掩膜層304a的側(cè)壁表面形成保護層307,所述保護層307的材料與第二掩膜層305a和停止層301的材料相同。所述保護層307用于保護第一掩膜層304a在后續(xù)刻蝕形成柵極層的工藝中,側(cè)壁不會被刻蝕減薄,以此保證了刻蝕形成的柵極層的特征尺寸精確易控。在本實施例中,所述第二掩膜層305a和停止層301的材料為氧化硅,因此所述保護層307的材料為氧化硅,所述保護層307的厚度為1?!?00埃,形成工藝為:采用等離子處理工藝處理所述第一掩膜層304a的側(cè)壁表面,使工藝中的氧氣等離子體與第一掩膜層304a內(nèi)的硅離子形成氧化硅,所述氧化硅即形成于第一掩膜層304a側(cè)壁表面的保護層307;所述等離子處理工藝為:壓力2毫托~100毫托,等離子體解離功率為100瓦~1500瓦,偏置電壓0~50V,氣體包含O2,氣體總流量1標準毫升/分鐘~1000標準毫升/分鐘,反應(yīng)時間5秒-200秒。在所述等離子處理工藝中,將氧氣解離成為等離子體,使所述氧氣等離子體帶有較高能量;所述第一掩膜層304a的材料為氮化硅,由于所述氧氣等離子體帶有高能量,能夠破壞氮化硅的化學(xué)鍵,產(chǎn)生硅離子和氮離子;等離子處理工藝中的氧離子能夠與所述硅離子構(gòu)成氧化硅材料,而被替代的氮離子隨著工藝過程中的氣流被帶走。而且,通過工藝參數(shù)的調(diào)節(jié),能夠使氧氣等離子體所帶的能量足夠打斷氮化硅的化學(xué)鍵;并且,通過工藝參數(shù)的調(diào)節(jié),能夠使所注入的氧氣等離子體積聚于所述第一掩膜層304a的側(cè)壁表面,更易于使氧離子與氮化硅中的硅離子生成氧化硅;此外,通過工藝參數(shù)的調(diào)節(jié),使所注入的氧氣等離子體積聚于所述第一掩膜層304a的側(cè)壁表面,使所形成的氧化硅厚度薄,因此所形成的保護層307的厚度薄,不會增大后續(xù)所形成的柵極層的尺寸。所述等離子處理工藝與各向異性的干法刻蝕工藝相似,且能夠在相同腔室內(nèi)進行,因此所述保護層307能夠在刻蝕第一掩膜層304a和第二掩膜層305a的腔室內(nèi)進行,能夠簡化工藝步驟;而且,所述等離子處理工藝所形成的保護層307厚度薄,在所述第一掩膜層304a的側(cè)壁表面形成保護層307不會使掩膜圖形尺寸發(fā)生明顯變化,使所述保護層307和第一掩膜層304a的尺寸不會影響后續(xù)刻蝕柵極薄膜303的工藝,能夠保證所形成的柵極層尺寸精確?,F(xiàn)有技術(shù)中,由于后續(xù)刻蝕柵極薄膜303的工藝需要首先保證對于第二掩膜層305a和停止層301具有較高的刻蝕選擇性,因此難以同時兼顧對于第一掩膜層304a的刻蝕選擇性,容易導(dǎo)致所述刻蝕工藝對第一掩膜層304a的刻蝕速率較高,導(dǎo)致所述第一掩膜層304a的側(cè)壁被刻蝕減薄,進而導(dǎo)致所述刻蝕工藝形成的柵極層的尺寸相較于設(shè)計尺寸偏小,因此所述柵極層的特征尺寸難以精確控制,晶體管的性能不良。因此本實施例中,需要在所述第一掩膜層304a的側(cè)壁表面形成保護層307。在本實施例中,后續(xù)的刻蝕工藝對所述第二掩膜層305a和停止層301的刻蝕選擇性較高,因此當所述保護層307和所述第二掩膜層305a的材料相同時,后續(xù)的刻蝕工藝對所述保護層307的刻蝕速度也較慢,所述保護層307能夠起到保護所述第一掩膜層304a側(cè)壁不被減薄,從而保證了刻蝕形成的柵極層的尺寸精確標準、且容易控制,進而使所形成的晶體管及半導(dǎo)體器件的性能穩(wěn)定。請參考圖7,在形成所述保護層307之后,在所述第二掩膜層305a表面形成第二光刻膠層308;以所述第二光刻膠層308和第二掩膜層305a為掩膜,刻蝕所述柵極薄膜303(如圖6所示),至暴露出停止層301表面為止,形成柵極層303a。所述第二光刻膠層308用于在刻蝕柵極薄膜303的過程中,保護所述第二掩膜層305a的表面不受損傷,并保持了所述第二掩膜層305a的形貌不發(fā)生改變,而且,所述第二光刻膠層308的圖形精確標準,進一步保證了刻蝕形成的柵極層303a的特征尺寸的精確度。所述第二光刻膠層308的形成工藝與形成第一光刻膠層306的工藝相同,在此不作贅述。所述刻蝕柵極薄膜303的工藝為各向異性的干法刻蝕工藝;在本實施例中,由于所述停止層301表面具有柵介質(zhì)薄膜302(如圖6所示),柵介質(zhì)薄膜302表面具有覆蓋薄膜(未示出),所述柵極表面303形成于所述覆蓋薄膜表面,因此,所述各向異性的干法刻蝕工藝在刻蝕所述柵極薄膜303之后,繼續(xù)刻蝕所述覆蓋薄膜和柵介質(zhì)薄膜302,直至暴露出停止層301為止;所述覆蓋薄膜刻蝕后形成覆蓋層(未示出),所述柵介質(zhì)薄膜302刻蝕后形成柵介質(zhì)層302a。所述柵極層303a的材料為多晶硅,在本實施例中,由于所需形成的晶體管具有高K柵介質(zhì)層和金屬柵極層,因此所述柵極層303a用于作為偽柵極層,為后續(xù)形成的金屬柵占據(jù)空間和位置。請參考圖8,在形成所述柵極層303a之后,去除所述第二掩膜層305a(如圖7所示),并在所述柵極層303a和第一掩膜層304a兩側(cè)的停止層301表面形成側(cè)墻309;以所述側(cè)墻309和第一掩膜層304a為掩膜對半導(dǎo)體襯底200進行離子注入,在柵極層303a兩側(cè)的半導(dǎo)體襯底300內(nèi)形成源區(qū)310a和漏區(qū)310b。在去除所述第二掩膜層305a的同時,去除所述第二光刻膠層308;所述去除第二掩膜層305a和第二光刻膠層308的工藝為濕法清洗工藝,能夠徹底去除第二掩膜層305a和第二光刻膠層308,并不會對柵極層303a造成損傷;在去除所述第二掩膜層305a之后,所述第一掩膜層304a用于作為形成側(cè)墻309時的掩膜,保護所述柵極層303a的表面不受損傷,保證了所述柵極層303a的形貌良好、尺寸精確。所述側(cè)墻309用于定義源區(qū)310a和漏區(qū)310b的位置,并在后續(xù)工藝中保護柵極層303a或金屬柵的側(cè)壁;所述側(cè)墻309的材料為氧化硅、氮化硅或氧化硅和氮化硅的組合;所述側(cè)墻309的形成工藝為沉積工藝,并在所述沉積工藝之后采用回刻蝕工藝暴露出第一掩膜層304a表面;因此,所述第一掩膜層304a的厚度需要根據(jù)刻蝕工藝而定,避免在所述回刻蝕工藝中,所述第一掩膜層304a被去除。本實施例中,在形成柵極層303a時,所述停止層301被保留,因此在形成所述源區(qū)310a和漏區(qū)310b時,所述停止層301還能夠用于保護半導(dǎo)體襯底300免受離子注入工藝的損傷,保證了晶體管的性能穩(wěn)定。請參考圖9,在形成所述源區(qū)310a和漏區(qū)310b之后,在所述半導(dǎo)體襯底300表面形成介質(zhì)層311,所述介質(zhì)層311的表面與第一掩膜層304a(如圖8所示)的表面齊平;在形成介質(zhì)層311之后,去除所述第一掩膜層304a和柵極層303a(如圖8所示),以形成開口(未示出);在所述開口內(nèi)形成金屬柵312。由于本實施例所需形成的晶體管為具有高K柵介質(zhì)層和金屬柵極層的晶體管,因此需要以金屬柵312替代所述多晶硅材料的柵極層303a。所述介質(zhì)層311的材料為氧化硅,所述介質(zhì)層311的形成工藝為:在所述停止層301、側(cè)墻309和第一掩膜層304a表面沉積氧化硅薄膜;采用拋光工藝,較佳的是化學(xué)機械拋光工藝去除高于第一掩膜層304a表面的氧化硅薄膜,形成介質(zhì)層311;所述第一掩膜層304的材料為氮化硅,與氧化硅之間具有選擇性,能夠在所述拋光工藝中,作為拋光工藝的停止位置。所述去除第一掩膜層304a和柵極層303a的工藝為刻蝕工藝,較佳的是濕法刻蝕工藝;所述金屬柵312的材料為銅、鎢、鋁或銀,所述金屬柵的形成工藝為沉積工藝,在所述沉積工藝之后進行拋光工藝,直至暴露出介質(zhì)層311為止。本實施例中,在所述第一掩膜層的側(cè)壁表面形成保護層,所述保護層的材料與第二掩膜層相同;由于所述第二掩膜層作為刻蝕柵極薄膜的掩膜,因此在所述刻蝕工藝中,所述保護層能夠保護所述第一掩膜層在刻蝕柵極薄膜的工藝中不被減?。凰瞿軌虮P蔚牡谝谎谀釉诤罄m(xù)刻蝕形成的柵極層時,避免所形成的柵極層尺寸縮小,因此使所形成的柵極層的尺寸符合設(shè)計標準,使所述柵極層的特征尺寸精確、且尺寸容易控制,所形成的晶體管的特征尺寸精確,保證了半導(dǎo)體器件具有良好的穩(wěn)定性。綜上所述,所述柵極薄膜表面具有第一掩膜層,所述第一掩膜層表面具有第二掩膜層;其中,所述第一掩膜層作為后續(xù)形成側(cè)墻時的掩膜,所述第二掩膜層作為刻蝕柵極薄膜的掩膜;在所述第一掩膜層的側(cè)壁表面形成保護層,且所述保護層的材料與第二掩膜層相同;由于所述第二掩膜層作為刻蝕柵極薄膜的掩膜,所述刻蝕柵極薄膜的工藝對于所述第二掩膜層具有較低的刻蝕速率,因此所述刻蝕工藝對所述保護層的刻蝕速率也較低;所述保護層能夠保護所述第一掩膜層在刻蝕柵極薄膜的工藝中不被減薄,從而保證了刻蝕后續(xù)形成的柵極層時,所形成的柵極層不會因為第一掩膜層的減薄而尺寸縮小,能夠使所形成的柵極層的尺寸符合設(shè)計標準;因此,所述柵極層的特征尺寸精確易控,使所形成的晶體管的特征尺寸標準精確,所形成的半導(dǎo)體器件的性能穩(wěn)定良好。進一步的,所述保護層的形成工藝為等離子處理工藝,所述等離子處理工藝的氣體為氧氣;在所述等離子處理工藝中,氧氣被解離成為等離子體,并通過工藝參數(shù)的調(diào)節(jié),使氧氣等離子體帶有足夠高的能量;由于第一掩膜層的材料為氮化硅,使所述氧氣等離子體所帶有的能量能夠破壞氮化硅的化學(xué)鍵,在所述等離子體處理工藝中,所述第一掩膜層的側(cè)壁表面能夠產(chǎn)生硅離子和氮離子;繼而,氧離子替代氮離子與所述硅離子構(gòu)成氧化硅材料,而被替代的氮離子隨著工藝過程中的氣流被帶走。而且,所述等離子處理工藝能夠使所注入的氧氣等離子體積聚于所述第一掩膜層的側(cè)壁表面,更易于使氧離子與氮化硅中的硅離子生成氧化硅,同時,使所形成的氧化硅厚度薄,即保護層的厚度薄,不會增大后續(xù)所形成的柵極層的尺寸,使所形成的柵極層的尺寸精確。本發(fā)明雖然已以較佳實施例公開如上,但其并不是用來限定本發(fā)明,任何本領(lǐng)域技術(shù)人員在不脫離本發(fā)明的精神和范圍內(nèi),都可以利用上述揭示的方法和技術(shù)內(nèi)容對本發(fā)明技術(shù)方案做出可能的變動和修改,因此,凡是未脫離本發(fā)明技術(shù)方案的內(nèi)容,依據(jù)本發(fā)明的技術(shù)實質(zhì)對以上實施例所作的任何簡單修改、等同變化及修飾,均屬于本發(fā)明技術(shù)方案的保護范圍。